When choosing ink for textile printing, you’re likely to encounter two main types: water-based ink and plastisol. Water-based inks are known for their soft hand feel and eco-friendly properties. They penetrate the fabric, dyeing the fibers for a print that moves with the fabric. Their makeup usually includes water as a solvent, but it’s important to note that some water-based inks may contain co-solvents, which can include petroleum-based substances.
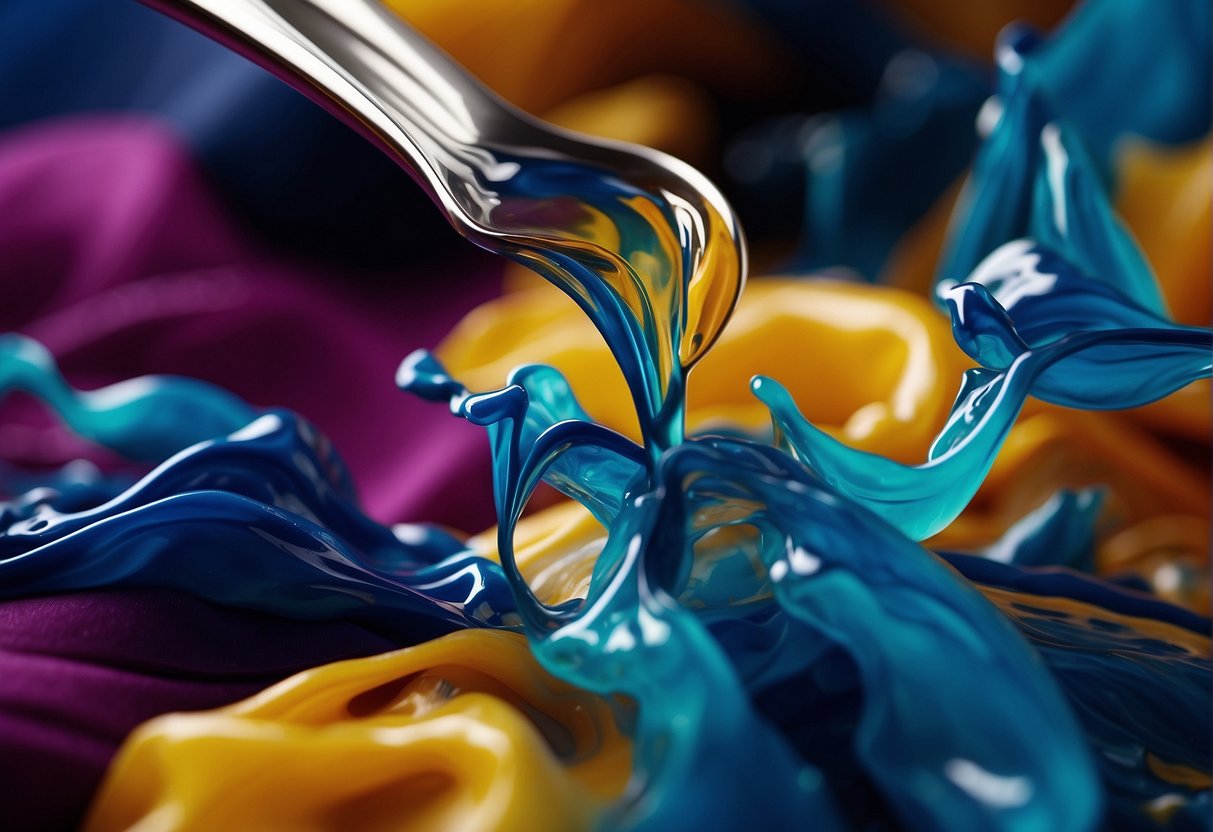
On the other hand, plastisol inks are the industry standard for vibrant prints that stand out on the surface of the fabric. The thicker consistency of plastisol is favored for its durability and bright, opaque colors. Unlike water-based inks, plastisol is composed of PVC particles and plasticizer, which means it sits atop the garment creating a layer over the fabric. This difference greatly influences the texture and breathability of the print, as well as the printing process itself.
Selecting between water-based and plastisol inks depends largely on the desired outcome, material of the garment, and the printing techniques available. Your choice will impact the feel, durability, and environmental footprint of the printed item, so understanding the characteristics and applications of each ink type is crucial for making an informed decision.
Overview of Screen Printing Inks
In screen printing, the choice of ink plays a pivotal role in the final output of your designs. Different inks offer varying qualities affecting durability, feel, and appearance of the printed material.
Distinguishing Water-Based Inks and Plastisol
Water-Based Inks: These inks penetrate the fabric, resulting in a softer feel. They are generally more eco-friendly since they’re free of PVC (polyvinyl chloride) and phthalates, allowing the ink to be air-dried or cured with heat. A key characteristic of water-based inks is their surface tension, enabling them to sit well on high-thread-count fabrics.
- Properties:
- Eco-friendly
- Soft-hand feel
- Heat or air-dried
Plastisol Inks: Plastisol is the go-to ink for screen printers who prioritize durability and opacity. Being a PVC-based system, plastisol provides a distinct texture on the fabric and requires heat to cure. Unlike water-based inks, plastisol doesn’t dry out in the screen, offering a longer working time.
- Properties:
- High durability
- Opaque finish
- Heat cured, not air-dryable
Historical Context and Evolution of Inks
Screen printing has a long history, and over time, the inks used have evolved significantly. Initially, screen printing was rudimentary, relying on basic dyes and inks. With advancements in technology, sophisticated inks like plastisol emerged in the 20th century, revolutionizing the industry with their ease of use and vibrant results.
- Early Inks:
- Simple dyes
- Limited colorfastness
- Modern Inks:
- Developed for specific substrates and purposes
- Better durability and color range
Through continued innovation, newer inks have been formulated to meet ecological standards while enhancing print quality. It’s your choice of ink that determines the look, feel, and sustainability of your screen-printed products.
Properties of Water-Based Inks
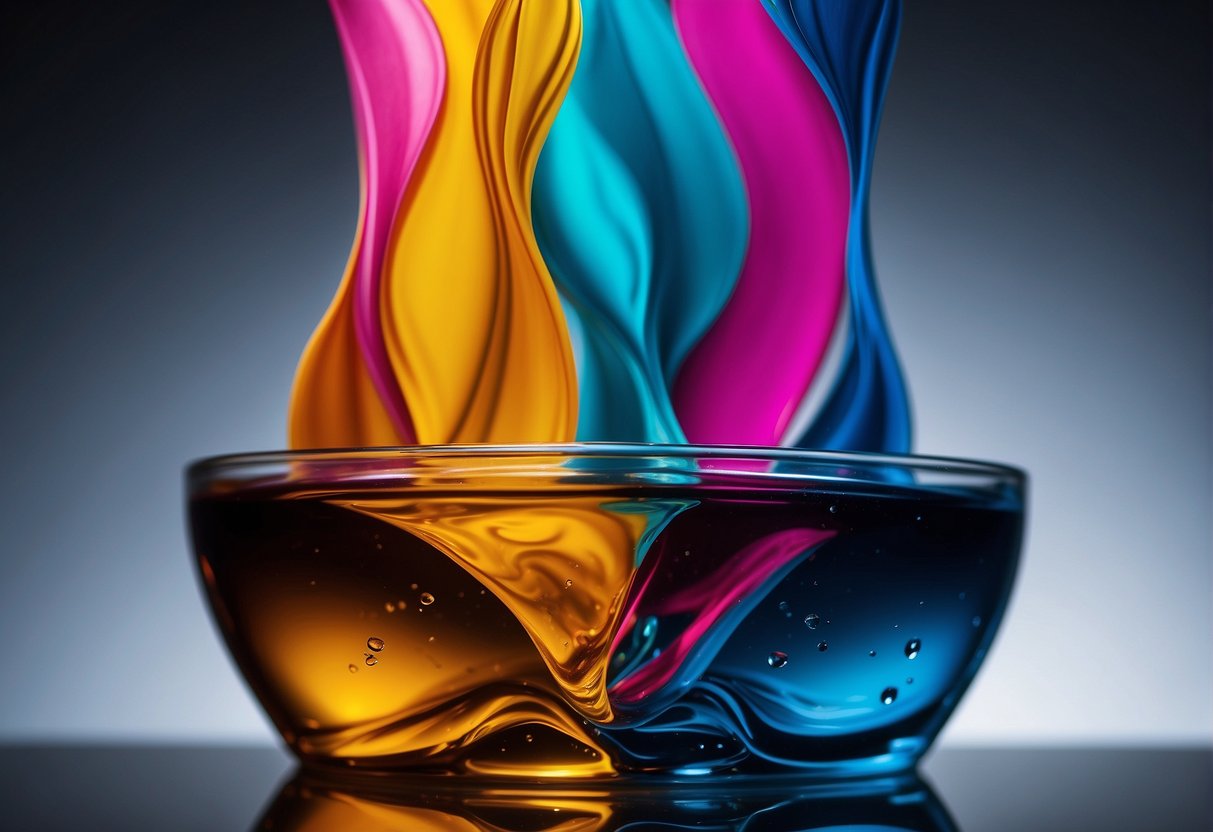
In this section, you will learn about the specific composition of water-based inks, why they are often considered user-friendly, and the reasons they might not always be the best choice for your printing needs.
Composition and Chemical Properties
Water-based inks primarily consist of a colorant such as dyes or pigments, and a solvent, which is usually water. They also contain binders to help the ink adhere to the printed material. Unlike plastisol inks, which are made of PVC and plasticizers, water-based inks are known for their eco-friendly properties due to their water solvent, which reduces the presence of volatile organic compounds (VOCs).
Advantages of Water-Based Inks
- Eco-Friendly: The use of water as a solvent makes these inks more sustainable and kinder to the environment.
- Breathable & Soft Hand: Water-based inks create a breathable print that maintains the original feel of the fabric, often referred to as a “soft hand.”
Disadvantages of Water-Based Inks
- Drying: These inks can potentially dry in screens if not cared for properly during the printing process.
- Limited Substrates: Less effective on certain non-porous substrates where the ink may not dry as well.
Characteristics of Plastisol Ink
Plastisol ink, known for its durability and vibrancy, is a preferred choice for textile printing. Explore its composition, advantages, and limitations to understand why it’s widely used in the screen printing industry.
Plastisol Composition
Plastisol ink is composed of PVC (polyvinyl chloride) resin and plasticizers that keep the ink in a liquid state before curing. It’s recognized as a 100% solid ink system, meaning it doesn’t have water or solvents that evaporate during the curing process. This composition classifies plastisol as a thermoplastic ink, which must be heated to a specific temperature to solidify.
Benefits of Using Plastisol
One of the main benefits of plastisol is its durability. Due to its PVC-based nature, plastisol ink can create prints that withstand multiple washes without fading. Its curing process involves heat, which causes the ink to fuse into a solid state, embedding the pigments firmly in the fabric. Additionally, plastisol’s brightness and vibrancy make it popular for creating eye-catching designs with a wide range of colors.
- Vibrant prints
- Excellent durability
- Suitable for various fabric types
Limitations of Plastisol Ink
Despite its advantages, plastisol ink’s PVC content can be a concern for those seeking environmentally friendly alternatives. It is not as breathable as water-based inks, and the texture can be heavier on the fabric. Furthermore, accurate curing requires precise timing and temperature control to avoid issues such as cracking or poor washability.
- Contains PVC, raising environmental concerns
- Heavier hand on the fabric after printing
- Requires proper curing to ensure durability
Comparison Between Water-Based Ink and Plastisol
When comparing water-based ink and plastisol, your primary considerations should include their curing processes, ease of handling, and environmental impact. Each ink type has unique characteristics that may affect your choice depending on the project requirements.
Curing Process and Techniques
Water-Based Ink: You’ll find the curing process for water-based ink involves evaporating water, requiring sufficient air circulation and heat. Commonly, you’ll cure these inks at a lower temperature of around 320°F (160°C) for a longer duration, which can affect the fabric less harshly.
Plastisol: Plastisol inks cure by reaching a higher curing temperature of around 320-330°F (160-165°C). The ink fuses into a solid layer when heated, offering durability and a crisp finish. You must ensure the entire ink film thickness reaches the cure temp to avoid durability issues.
Handling and Usage
Water-Based Ink:
- Ease of Use: These inks have a thinner viscosity, making them easier to work with for detailed designs.
- Clean-Up: Cleaning screens and equipment is typically easier with water-based inks as they can be cleaned with water.
Plastisol:
- Ease of Use: Often favored for its ease of printability and ability to stay wet on the screen for extended periods.
- Clean-Up: Requires solvents for clean-up, which can be challenging and necessitate the use of specialized chemicals.
Environmental Considerations
Water-Based Ink:
- Eco-Friendly: These are considered more eco-friendly due to their water solubility, lower VOC emissions, and often non-toxic nature.
- Environmental Impacts: They generally have a smaller environmental footprint, given their composition and clean-up requirements.
Plastisol:
- Eco-Friendly: Typically contains PVC and phthalates, which are subject to scrutiny for their environmental impact.
- Environmental Impacts: Can require more potent solvents for clean-up, contributing to VOC emissions and requiring more care with disposal.
Both water-based inks and plastisol provide vibrant colors, but the vibrancy can differ with the ink’s opacity. Water-based inks may offer a softer look with vibrant colors absorbed into the fabric, while plastisol tends to sit on top of it, giving a more raised feel and potentially higher opacity. Your choice between these inks will significantly depend on the durability required, the cure process you can support, and your environmental priorities.
Practical Applications in Screen Printing
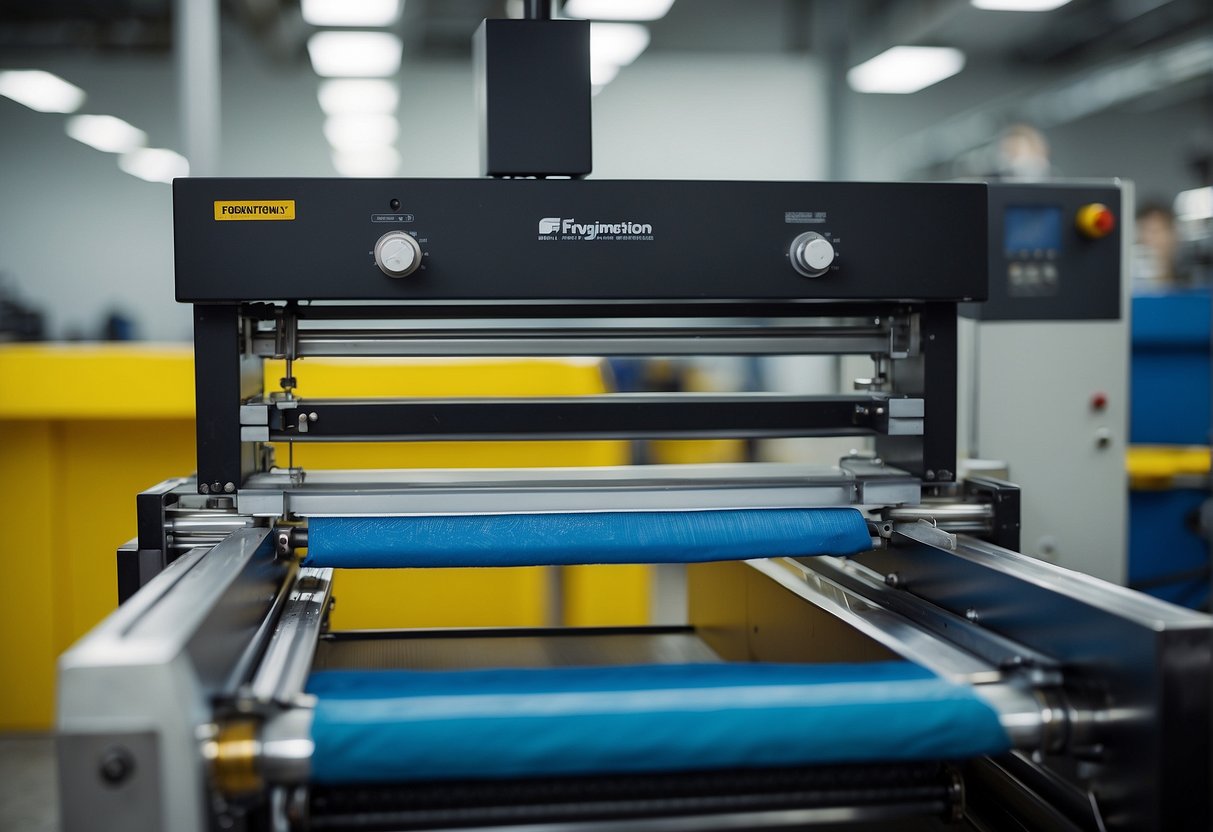
Screen printing offers a versatile way to embellish a variety of fabrics, whether you’re aiming for vibrant designs on t-shirts or seeking a specific texture on apparel. The choice between water-based and plastisol inks dramatically affects fabric interaction, design longevity, and the tactile feel of the final print.
Suitability for Different Fabrics
- Cotton: Water-based inks are ideal for cotton fabrics, as they are absorbed into the fibers, creating a soft-to-the-touch feel and enhancing breathability. In contrast, plastisol inks sit on top of the fabric, making them suitable for dark-colored shirts and providing a smooth, plasticized texture.
- Polyester and Nylon: Plastisol inks adhere better to synthetic materials such as polyester and nylon, reducing the chance of dye migration, which can occur with water-based inks on these fabrics.
- Tri-blend T-shirts: For tri-blend t-shirts, which combine cotton, polyester, and rayon, both ink types can be used, but the outcome will vary: plastisol will give a bold, solid feel, while water-based inks will offer a more vintage look and feel.
Achieving Specific Effects and Finishes
- Bright Colors and Detailed Design: Plastisol inks are renowned for their ability to create bright colors and maintain detailed design elements, even on darker fabrics. They provide a consistent and opaque finish, which is ideal for designs that demand high impact and clarity.
- Breathable and Vintage Effects: Water-based inks excel in creating breathable prints with a vintage look, as they dye the fabric itself and preserve its natural texture. This effect is especially sought after in casual and fashion-forward apparel, where a less pronounced feel is desirable.
The choice between water-based and plastisol inks in screen printing is determined by the desired outcome on the fabric as well as the specific requirements of the print job. You’ll need to consider the type of fabric, the desired feel, and the longevity of the print when selecting your ink.
Technical Considerations for Print Shops
When choosing between water-based ink and plastisol for your print shop, your decision impacts equipment requirements and the chemicals you’ll work with. The technical factors from mesh selection to dryer type fundamentally affect your printing process and final product.
Equipment and Screen Mesh
- Screen Mesh: For water-based inks, use a higher mesh count to facilitate a softer print and prevent ink from drying in the screen, a common issue due to the ink’s lower viscosity. Screen types between 305-355 mesh typically yield the best results. Conversely, plastisol inks, with their thicker viscosity, generally require a mesh count in the 110-160 range for optimal coverage and ease of print.
- Forced-Air Dryer: Your drying equipment plays a crucial role. Water-based inks demand a forced-air dryer to facilitate evaporation, which is essential due to the water content in the ink. On the other hand, plastisol inks cure through a heat-induced reaction and are less dependent on air movement, giving you flexibility in choosing between a standard or forced-air system.
Ink Modifiers and Additives
- Additives and Modifiers: With water-based inks, you might need to incorporate additives to prolong the ink’s open time and prevent it from drying on the screen. Acrylics are sometimes used to enhance the durability of water-based prints.
- Viscosity Adjustments: Plastisol inks offer the simplicity of being ready to use straight from the container, but they may also be modified with additives to change viscosity or gloss. When adjusting the viscosity, you enable finer detail and improved penetration into the fabric for a softer feel.
Remember to always adjust your additives carefully; each increment alters the ink behavior and the outcome of your prints. Your equipment and screen mesh choices, alongside the modifiers you use, are pivotal in achieving the desired effects and efficiency in your print shop.
Health and Safety Factors
When comparing water-based inks and plastisol, it’s essential to consider the health and safety factors that affect you, your workspace, and the environment. These factors include exposure to chemicals, solvents, and other substances that may pose risks.
Regulations and Compliance
Water-based inks offer a more eco-friendly option largely because they’re free from phthalates and PVC. They comply with stricter environmental regulations due to their lower VOC (Volatile Organic Compounds) emissions. This means they have fewer fumes, reducing your exposure to potentially harmful solvents.
On the other hand, plastisol inks contain plasticizers and PVC, which can release harmful chemicals during the curing process. The use of plastisol inks requires adherence to specific safety measures to mitigate potential health risks, such as adequate ventilation.
Non-Toxic Alternatives
Seeking non-toxic alternatives is beneficial for both personal health and the planet’s well-being. Water-based inks are often preferred as they are usually free from formaldehyde and heavy metals. Brands have developed sustainable and eco-friendly water-based ink options that minimize environmental impact.
Conversely, to address the issue of plastisol inks containing chemicals of concern, manufacturers are exploring phthalate-free and non-PVC plastisol inks. It’s crucial to ensure that the alternatives you choose meet the industry standards while also aligning with your commitment to safety and sustainability.
Maintaining and Enhancing Print Quality
To achieve the best results in print quality, you need to consider the characteristics of the inks you choose and understand their behavior on various fabrics. Whether you’re aiming for soft hand designs with vibrant colors or durable prints that resist fading, the right choice and application of ink are critical.
Ink Penetration and Fixation
Water-based inks: They are known for their ability to deeply penetrate fibers, which often results in a print with a soft hand. Perfecting your design begins with understanding that water-based inks require thorough curing to set the ink and prevent fading. For optimal color vibrancy and washability, follow the ink manufacturer’s recommended cure times.
Plastisol inks: Unlike water-based inks, plastisol remains on top of the fabric, creating a layer that is more resistant to wear. Achieve more vibrant prints with accurate color matching through proper curing, which is necessary to prevent cracking or peeling.
Longevity of Printed Apparel
Your printed apparel’s durability and longevity significantly depend on the ink’s interaction with cleaning agents and its resistance to the rigors of regular wear.
- Water-based inks: When cured properly, they can offer excellent durability and feel comfortable against the skin. Using the correct detergents that are gentle on the fabric will help maintain the crispness of the design.
- Plastisol inks: For longevity, ensure that the printed apparel avoids harsh cleaning cycles, as the plastisol layer can deteriorate faster under intense wash conditions. Remember that a high-quality plastisol print should resist fading, but proper care is key.
Consumer Preferences and Market Trends
As you navigate the printing industry, you’ll see that consumer demand heavily influences market trends, especially in the debate between water-based inks and plastisol. Two significant aspects shaping these trends are the growing insistence on eco-friendly choices and the expectation of high-quality textures and hand feels from the finished products.
Demand for Eco-Friendly Options
Consumers are increasingly aware of the environmental impacts of their purchases. This has led to a surge in the demand for eco-friendly printing materials. Water-based inks are typically seen as a more sustainable option, as they are free from harmful solvents and are easier on the environment during the cleanup process. You might appreciate their better color accuracy and the way garments printed with these inks allow for better breathability.
Popularity of Specific Textures and Hand Feels
The feel of a printed fabric is crucial to the consumer experience. Water-based inks are celebrated for their soft hand feel, which is highly desired in the fashion industry. This softness allows for a more natural drape of the fabric, enhancing the wearer’s comfort. Plastisol, while known for its durability, presents a stiffer feel, which could be a disadvantage if you’re targeting markets that favor comfort. However, if you’re looking to produce vivid, graphic-heavy designs, plastisol’s texture might be just what you need for that bold statement.
With this knowledge, you should feel confident your printing choices will align with both current consumer preferences and overarching market trends.
Future Directions in Ink Technology
As you explore the advancements in ink technology, you’ll discover significant innovations focused on sustainability and environmental friendliness, anticipating the needs of a more eco-aware market.
Innovations and Developments
Ink technology has continuously evolved, with recent innovations aiming to enhance not only the quality and durability of prints but also their compatibility with digital printing techniques. Water-based inks have made strides, particularly in the domain of inkjet printing, overcoming challenges associated with drying time and ink-substrate interaction. These advancements suggest a shift away from traditional PVC plastisols, which have been predominant in screen printing due to their ease of use and vibrant colors. Innovations in ink formulations are pushing the boundaries of what’s possible, with research hinting at the future role of water-based inks in high-definition and precise printing applications.
- Precision: New ink technologies provide finer detail and higher resolution.
- Speed: Improved drying times for water-based inks are reducing production bottlenecks.
Sustainable and Eco-friendly Advancements
The push for sustainable solutions has catalyzed the development of eco-friendly inks. Water-based inks are at the forefront here, minimizing the environmental impacts traditionally associated with solvent-based inks. These inks do not release volatile organic compounds (VOCs) into the atmosphere, making them better for the health of print shop workers and the environment. Additionally, ongoing research into biodegradable inks and recyclable materials (Technological barriers to digital printing in textiles: a study) promises a future where print products have a smaller ecological footprint.
- Low VOCs: Environmentally friendly inks that reduce harmful emissions.
- Recyclability: Advances in making printed materials easier to recycle.
Choosing the Right Ink for Your Project
When embarking on a printing project, two prominent types of inks to consider are water-based inks, known for their ease of use and eco-friendliness, and plastisol inks, recognized for their vibrancy and coverage. Your selection can significantly impact cost, quality, and the production process of your printed materials.
Factors to Consider When Selecting Ink
- Cost: Water-based inks can be less expensive and are easier to clean up, reducing labor costs, whereas plastisol inks may require additional cost for solvents and cleaners.
- Opacity: Plastisol offers high opacity, making it suitable for dark garments. However, water-based inks have a softer hand and can be more transparent.
- Viscosity: Plastisol is thicker and sits on top of the fabric, and water-based ink penetrates the fabric, influencing your choice depending on the desired outcome.
- Co-solvents: These may be necessary with water-based inks to keep them from drying too fast.
- Vibrant Colors: Plastisol inks are excellent for bright and vivid colors, especially on darker fabrics.
- Ideal Print: You’ll achieve a softer feel with water-based inks; for a more raised texture, plastisol is preferable.
- Versatility: Water-based inks may be better for certain types of fabric like light cotton shirts, while plastisol excels in various other applications such as towel printing and roll-to-roll yardage printing.
Cost-Benefit Analysis
- Efficiency: For bulk orders, plastisol’s ease of use could offset its higher initial cost due to its capacity for faster production speeds.
- Durability: Plastisol inks have a reputation for lasting longer without fading, potentially reducing the need for reprints.
Utilizing the above knowledge confidently, you can consider each aspect and determine the most efficient and cost-effective choice for your printing needs, ensuring your project’s success with the correct ink selection.
Frequently Asked Questions
The following FAQs address the intricacies of using water based and plastisol inks in screen printing, including their benefits, composition, environmental impact, printing challenges, and efficiency.
What are the benefits of using water based ink for screen printing?
Water based inks are renowned for their eco-friendly properties and soft hand feel. They absorb into the fabric, creating a print that moves with the garment, making them ideal for designs requiring a more natural look.
What are the main differences between water based ink and plastisol ink in terms of print quality and durability?
Water based inks offer a softer print quality with a more subtle texture, while plastisol inks provide a vibrant, crisp image that sits on top of the fabric. Plastisol tends to be more durable and resistant to fading through multiple washes compared to water based inks.
How is plastisol ink composed, and what implications does its composition have for its use in printing?
Plastisol ink consists of PVC particles suspended in a plasticizing emulsion, creating a heavy-bodied ink. This composition requires heat to cure and results in a durable, raised print that is less breathable than water based prints.
Can you explain the environmental impacts of using plastisol versus water based inks?
Plastisol inks contain PVC and phthalates, substances with potential health and environmental concerns. Water based inks are considered more environmentally friendly, as they are free from PVC and phthalates, and clean up with water.
What are some common challenges printers face when using water based inks, and how can they be mitigated?
Challenges with water based inks include their tendency to dry quickly in screens, leading to clogging. This can be mitigated by keeping screens flooded with ink and using retarders to slow down drying time.
In terms of ease of use and efficiency, how do water based inks compare with plastisol inks for t-shirt printing?
Water based inks require more skill to print effectively, as they can dry in the screen and require proper curing to achieve durability. Plastisol inks are user-friendly due to their ease of use and straightforward curing process, making them a popular choice for many printers.